Greybox models for in-situ quantification of probabilistic tool life of CVD coated carbide hobs
Within the priority program SPP2402 "Greybox models for the qualification of coated tools for high-performance machining", the competences of materials and machining technology are brought closer together. We conduct research together with the WZL of RWTH Aachen University in the process of hobbing.
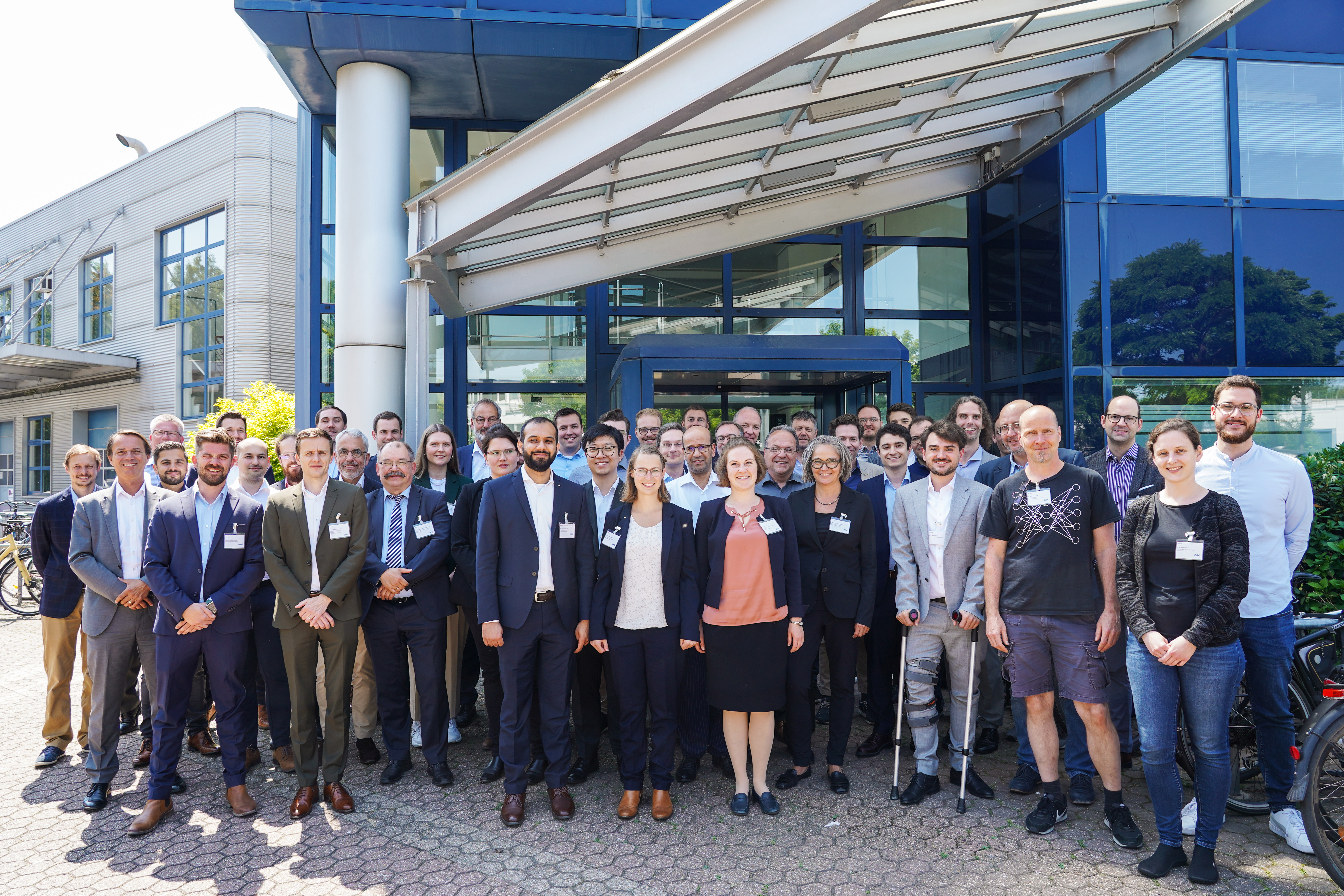
Problem
Gear hobbing is an established process for gear manufacturing. The load spectrum in gear hobbing leads to abrasive tool wear, which, when increased, negatively affects the dimensional accuracy of the workpiece as well as the stability of the tool cutting edge. Local inhomogeneities in the microstructure of the hard material coating and substrate as well as varying parameters in the coating microstructure result in probabilistically distributed service lives, which change in-situ depending on the real, complex operating conditions. By predicting the remaining service life of a tool depending on the material strength and the stress during machining, the total service life of coated tools can be significantly increased by closed-loop control. To date, the onset of failure, wear progress and remaining service life cannot be identified or predicted with sufficient certainty either by modeling or experimentally.
Objective
The overall objective of the project is to describe in detail the thermomechanical tool load and the resulting tool wear during hobbing by using deterministic models coupled with in-situ acquired process data, thus allowing a lifetime optimized control of the process. We are working on creating an integrative greybox model for predicting the tool life of CVD-coated carbide tools.
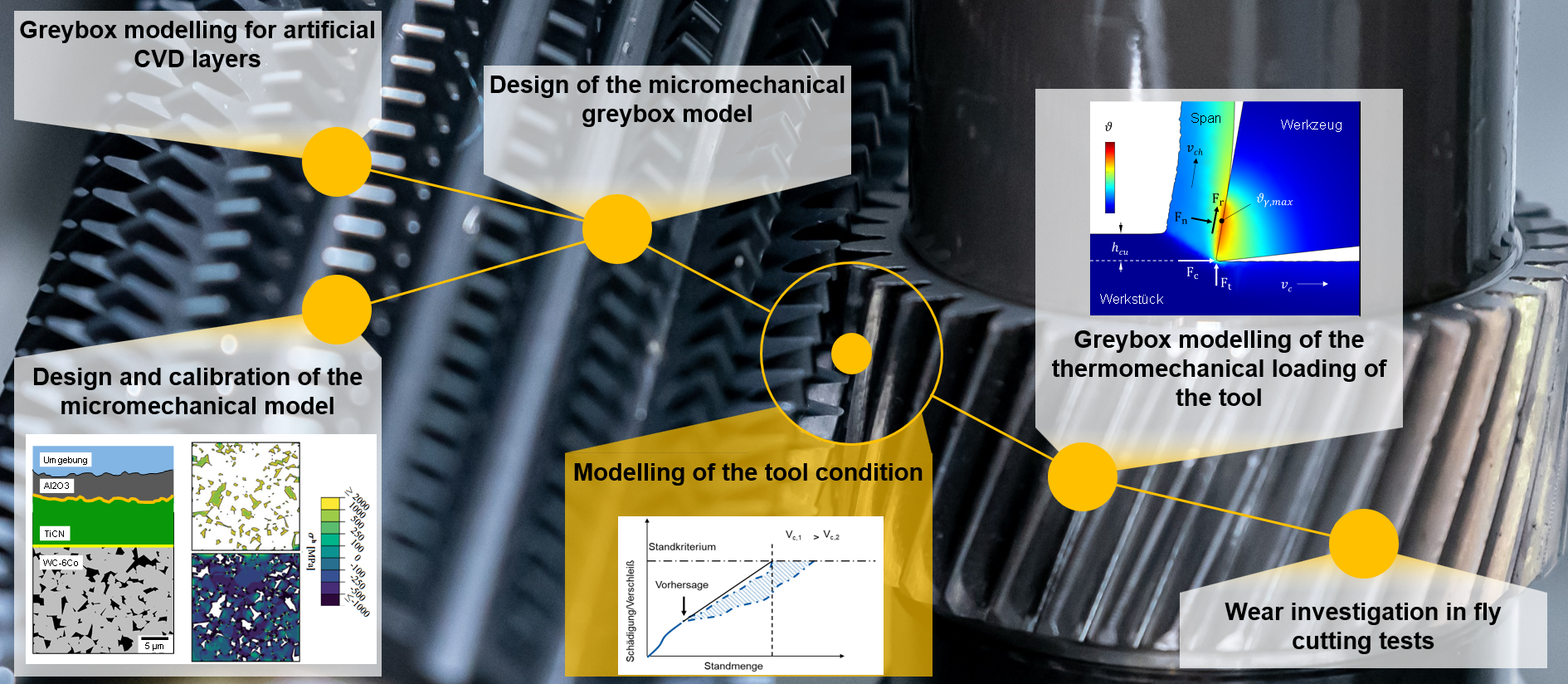
Project partners
Laboratory for Machine Tools and Production Engineering (WZL) of RWTH Aachen University
Funding
DFG SPP 2402 Greybox models to qualify coated tools for high performance machining
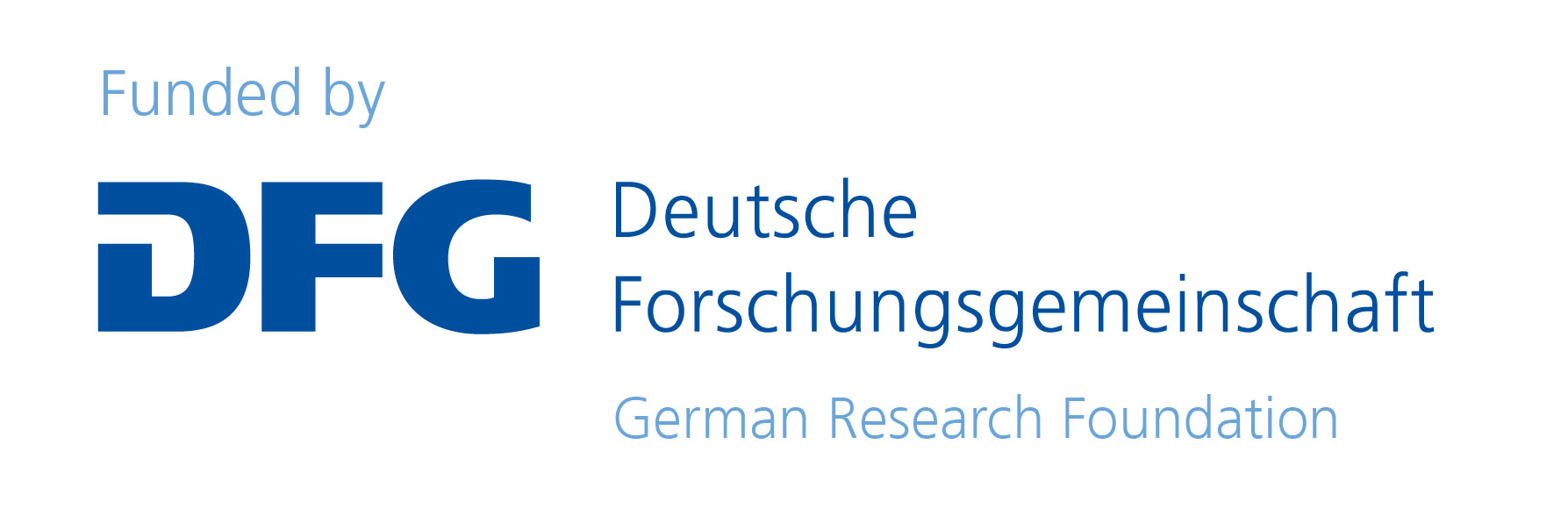